Curious if your machine can go electric?
The answer is yes.
And it’s easier than you think. From excavators to sweepers and from rollers to robots. With today’s technology, nearly every diesel-powered machine can be converted to a clean, quiet, fully electric version. We’ll show you what’s possible, how it works, and how to get started.
✅ Step-by-step guide through the process
✅ What to consider when getting started
✅ Tool to calculate how many kWh fits your machine can hold
✅ Real-world benefits and technical examples
Ready to explore your options?
Start by learning how the process works, or jump straight to our capacity calculator.
Why go electric?
Authorities across Europe are rapidly tightening emission rules. In many cities, diesel engines are already restricted, or banned entirely. Public tenders now favor or even require zero-emission machinery. But there’s more at stake than compliance. Electric machinery brings powerful business advantages.
10 Powerful Benefits of converting to electric
- Zero emissions: No nitrogen, particulates or CO₂
- Sustainable performance: 50–70% lower environmental cost
- No fuel costs: Electricity is cheaper: no idling losses
- Near-silent operation: Less noise, fewer vibrations
- Indoor use: Clean and safe for indoor environments
- Work longer hours: No sound restrictions in urban areas
- Low maintenance: Fewer moving parts, lower wear
- Fast inspections: Less downtime, less complexity
- Higher margins: Win tenders with clean tech
- Government incentives: Subsidies and tax breaks
Electric motors offer up to 50% lower operating costs. And battery technology is improving fast.
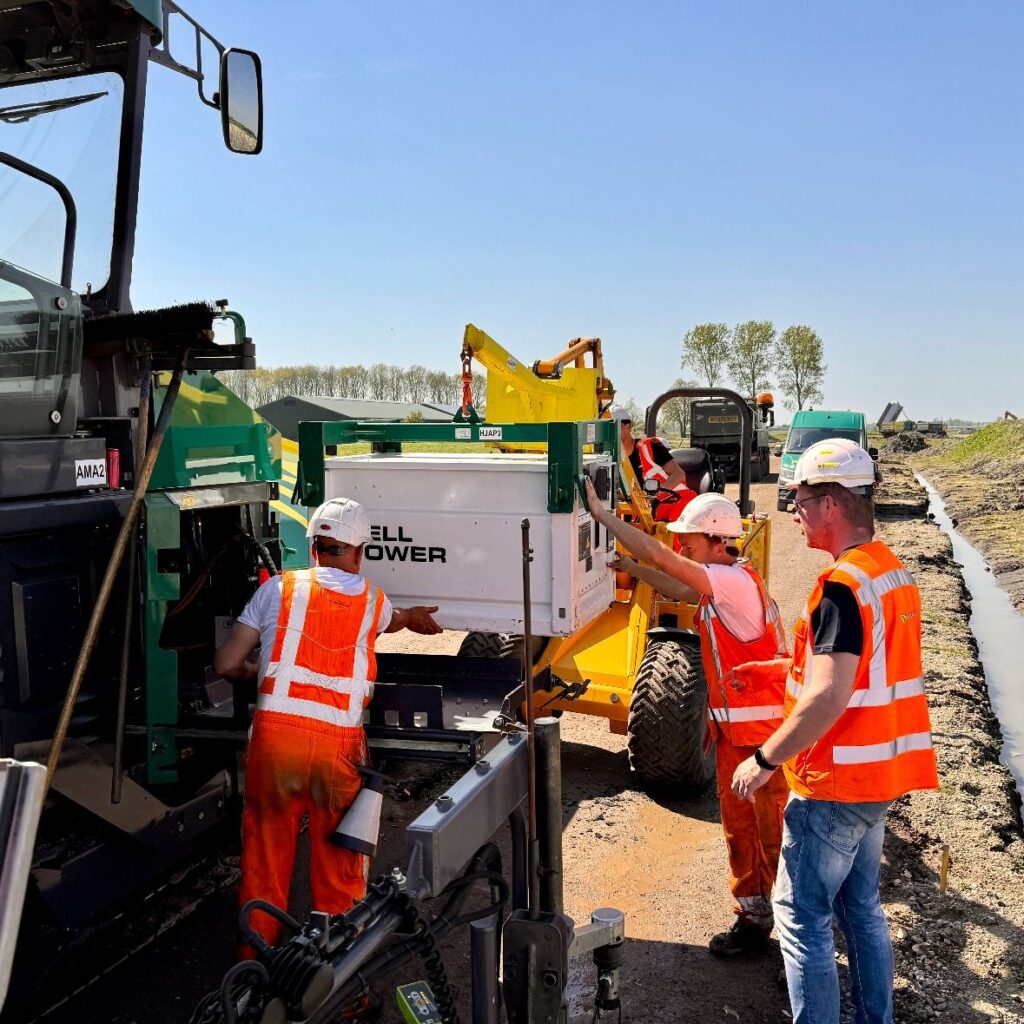
Battery innovations
drive electrification forward
Converting a diesel machine to electric means replacing the engine and fuel tank with a battery and electric drive system. Today’s batteries are up to 60% smaller and much more powerful than older types. That means more capacity, less weight, and enough power for a full workday.
- A 23-tonne excavator can now be fully electrified
- Custom batteries can run in extreme cold or dusty conditions
- Specialized batteries last up to 30,000 charge cycles
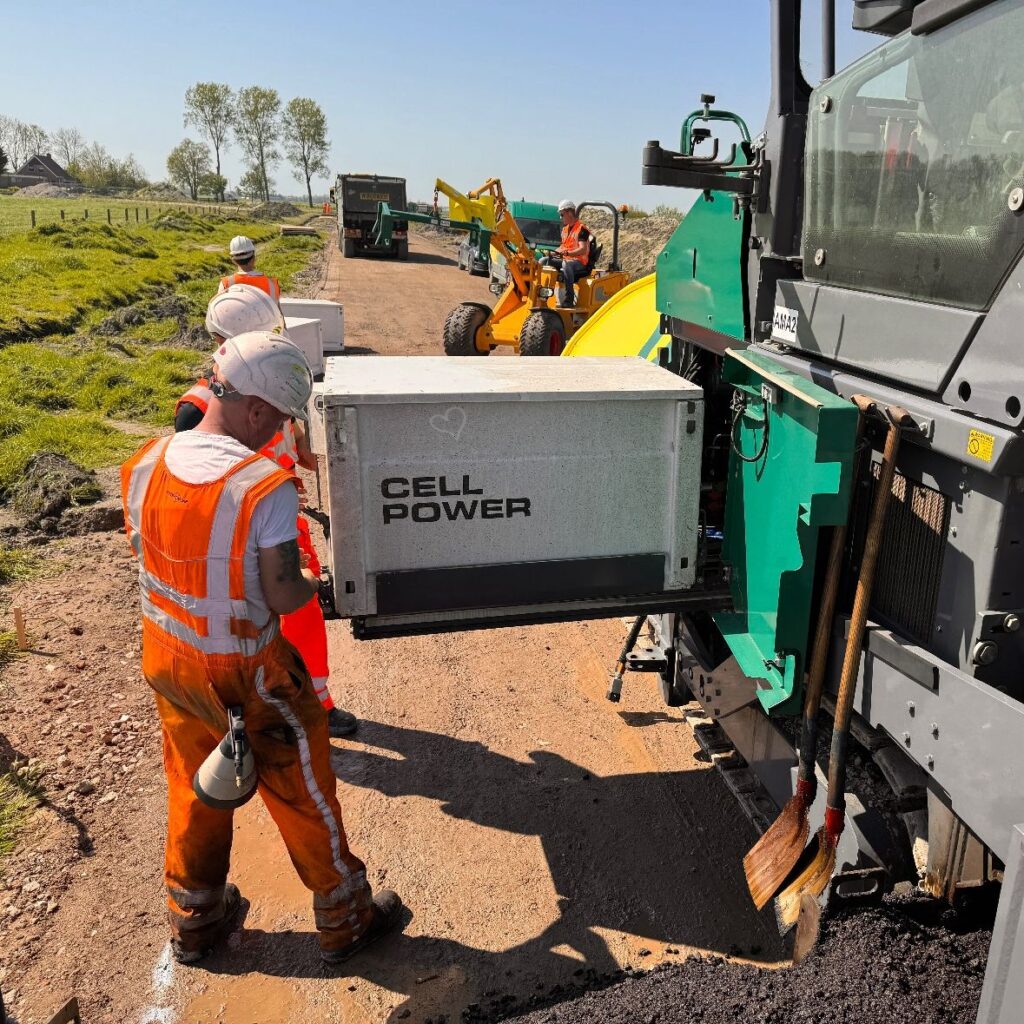
Step-by-step guide: from diesel to electric
Thinking about converting your diesel-powered machine to electric? Smart move. But where do you start?
This step-by-step guide shows you what to expect and what to consider.
- Identify your current machine
Which machine are you converting? Note the brand, model, year, and its typical use. This is the foundation of your conversion plan. - Determine power and energy needs
How much power does the machine use under normal load? How many operating hours per day? This helps calculate how much battery capacity you’ll need. - Determine your charging concept
Are you able to charge overnight with the batteries still in the machine? Or do you need a swappable battery pack so you can keep working while charging? - Check available space for the battery
Where can the battery go? Look at areas like the fuel tank or engine compartment.
Use our Capacity Calculator to estimate how many kWh would fit in the available space. - Select the right motor and battery
Based on space, power needs, and daily use, choose an electric drive system and battery pack that fits your machine. - Choose or design a conversion kit
Some machines have ready-made kits. If not, custom solutions are possible. We help with both. - Perform or outsource the conversion
Have your own workshop? Great! Otherwise, we can connect you with a certified retrofit partner. - Testing and commissioning
Once installed, the system is tested for safety and performance. Then you’re good to go.
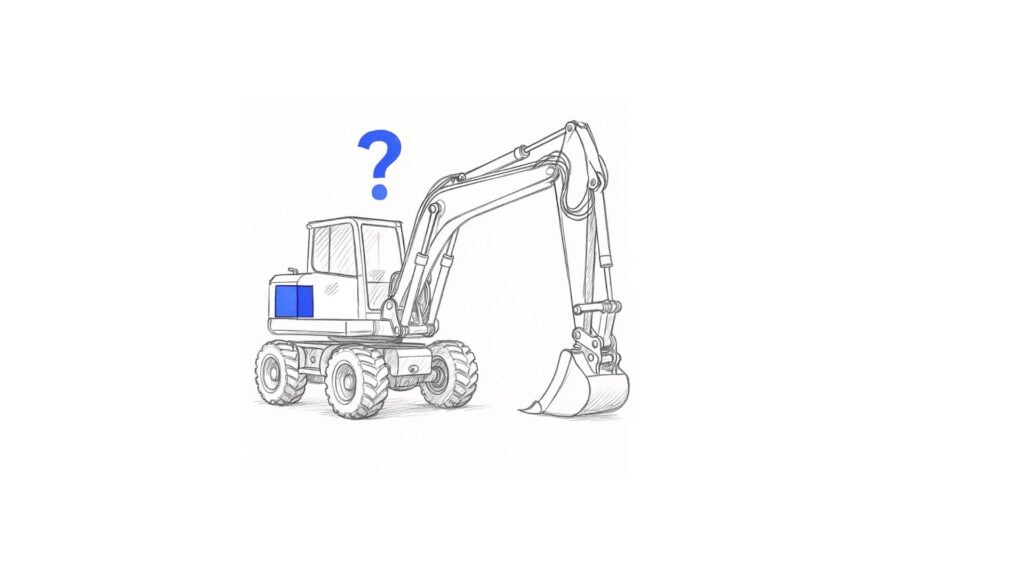
Capacity Calculator
Curious how many kWh would fit into your machine? Give us some information about the available space and our free Capacity Calculator gives you the answer.
What machines can be converted?
Thanks to custom battery design, almost any type of machine can be electrified. We’ve built solutions for:
- Excavators and loaders
- Asphalt warmers and road rollers
- Tool carriers (spraying, mowing, sweeping)
- Cleaning equipment
- Agricultural and manure systems
- Foundation rigs – even forklifts in cold storage
We design on a cell level instead of modules, this saves space and increases capacity.
Real world examples:
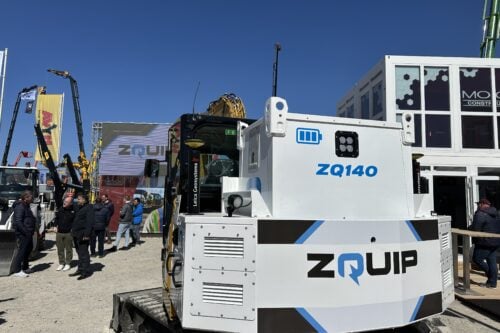
We are proud to announce that we are starting the production of new battery energy modules for the construction industry. Developed by ZQuip, these modules use our advanced …
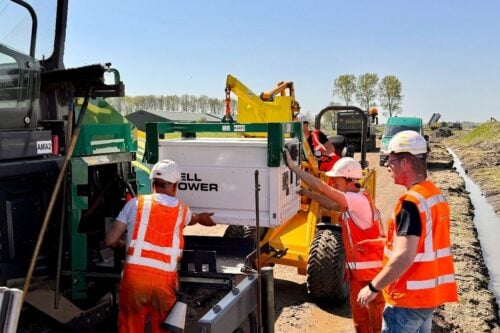
The road construction industry is in a state of flux. Motrac Industries, with the support of Intercel, has developed an all-electric asphalt set that represents an important step …
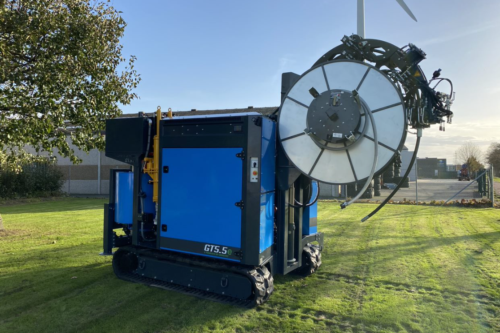
The transition to emission-free construction machinery continues. Gomutec, developer of machines for installing heat loops in the ground, has successfully tested its first electric grout machine, the GT …
Costs of converting from diesel to electric
Converting a diesel machine to electric requires investment, but luckily the return is fast:
- Average payback time: 7 years (often shorter)
- Savings on fuel, maintenance, and time
- Gain competitive advantage in tenders
- Access to subsidies and tax benefits
“Every diesel machine running today will need to be replaced in the coming years. Start early and stay ahead of your competition.”
Why work with Intercel?
With over 35 years of experience in battery innovation, Intercel offers:
- In-house engineering & custom design
- Battery production in The Netherlands
- Batteries built on cell level = more efficient use of space
- Fully pre-tested and ready-to-use on delivery
- Personal guidance and co-engineering from concept to completion
- Extensive aftersales and service
We’ve helped clients electrify some of the most demanding machines in Europe. Now we’re ready to help you.
Technical highlights of our battery systems
- Lithium-based: LiFePO4, LTO, NMC
- 10% charge, 95% depth-of-discharge
- Up to 30,000 cycles
- Charging below 0°C possible
- Special dimensions & high energy density
- Interfaces: RS232, CAN bus, MOD bus, Wi-Fi, Bluetooth
- Built in the Netherlands, ISO 9001 certified
- Systems from 3.2V to 1000V – 500Wh to 1MWh
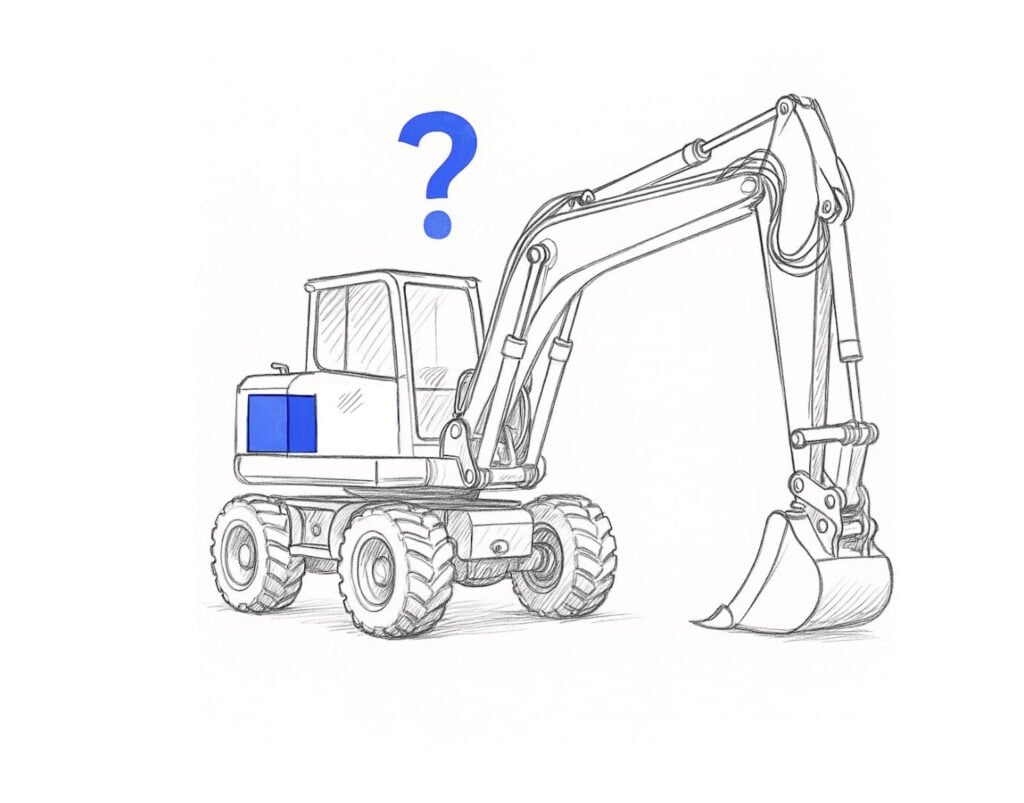
How many kWh would fit in your machine?
How can Intercel help you convert from diesel to electric?
Intercel Intercel has the ability to design a solution for any application that requires a custom battery. With an in-house engineering department and more than 30 years of experience in the battery industry, no challenge is too great. We build an all-in-one solution. Compared to our competitors, we offer the following advantages:
- Optimal use of the available space
- No imbalance between modules
- Charge faster, discharge deeper
- Much shorter installation time, the battery is delivered ready to use
- Quality guarantee, production according to ISO 9001
- Direct contact with the producer
- High-quality electronics
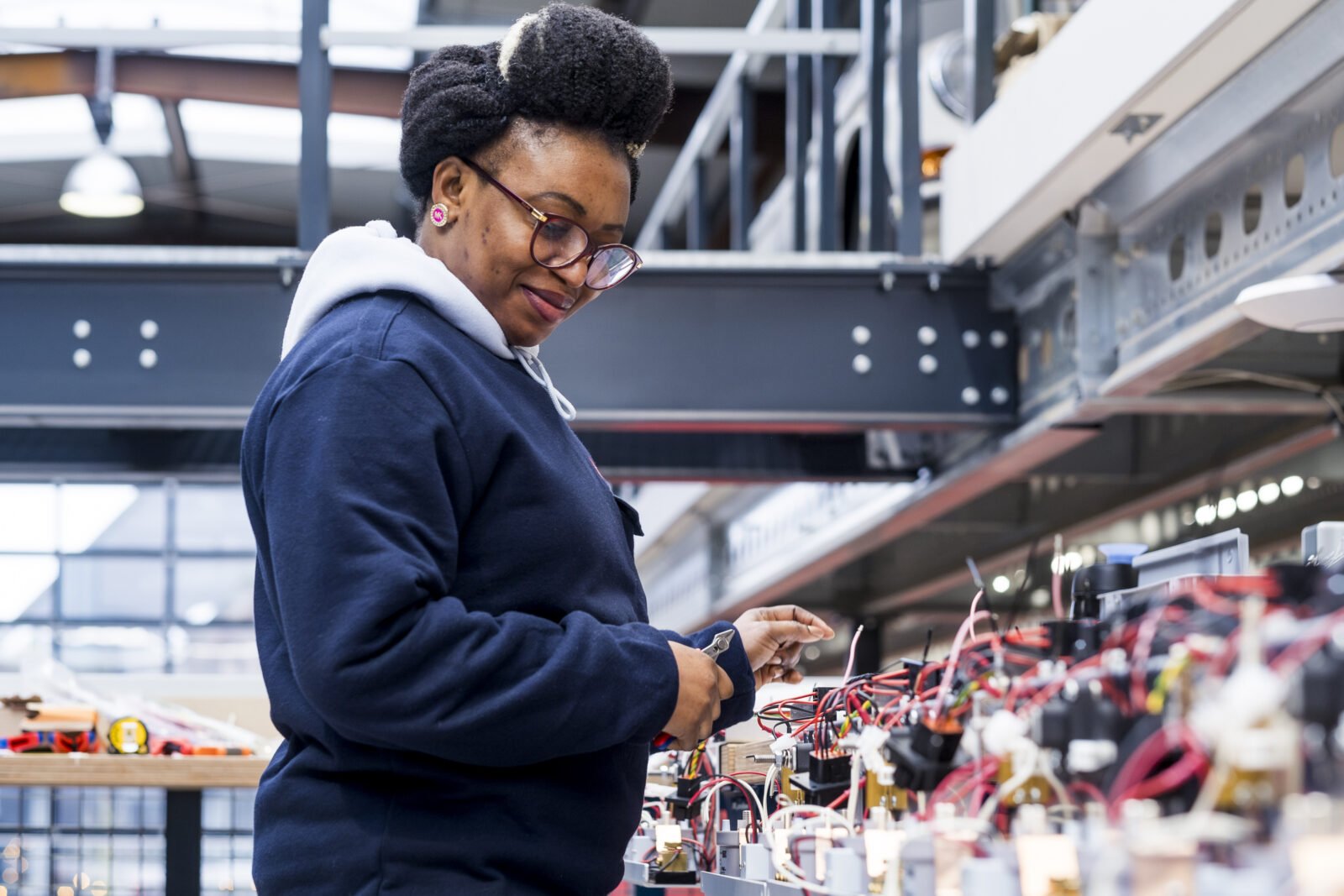
"*" indicates required fields