Innovation in construction with electric HPU
Sustainability and technological advancement are the foundation of the collaboration between Vigor Piling and Intercel Electrification. The electric Hydraulic Power Unit (HPU) is a prime example of how innovation is transforming the construction sector to enable the energy transition. What were the unique challenges, the collaborative approach, and the strong results of this partnership?
The challenge
Driven by increasing regulations aimed at sustainable building, Vigor Piling develops an entirely electric HPU in-house. This regulation compels the construction sector to adopt greener methods. As a specialist in foundation techniques, Vigor Piling designs and builds an electric HPU for BAM as an innovative replacement for traditional diesel-driven HPU’s of pile driving machines. The challenge is to develop a powerful battery component within the existing design frameworks that is optimally balanced with the electric drive and provides sufficient power and endurance.
Vigor Piling has been a prominent player in the foundation industry since 2018, specializing in the development and production of Hydraulic Power Units (HPU’s) for construction and offshore. The core activity is complete in-house development and construction of HPU’s. Theo Mastenbroek, Engineer and Project Manager at Vigor Piling, designs HPU’s in direct consultation with the client. With two halls for metalworking and assembly, Vigor Piling designs and assembles everything itself, from casing to electrical diagrams, allowing for a high degree of customization and quality control.
The location of Intercel in Haarlem ensures easy communication and an efficient collaboration where Intercel not only meets the technical requirements but also delivers a turn-key battery pack that perfectly fits our application
Theo Mastenbroek – Engineer and Project Manager Vigor Piling
Collaborative approach
While Vigor Piling has extensive experience with HPU’s, the expertise of Intercel Electrification is crucial for the development of the electric HPU. With over 35 years of experience in the battery industry, Intercel develops a custom-made battery pack that meets the needs of Vigor Piling. R&D engineer and project manager Theo Mastenbroek speaks highly of the collaboration: “The proximity of Intercel in Haarlem ensures quick communication and an efficient collaboration, where Intercel not only meets the technical requirements but also delivers a turn-key battery pack that perfectly fits our application.”
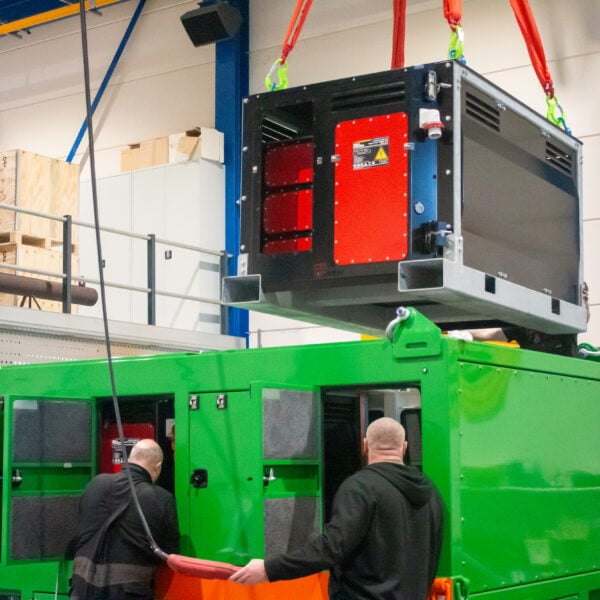
The solution
The result is a fully electrically driven HPU, equipped with two battery packs of 250 kWh each. This allows a hydraulic impact hammer to work for 6 hours without needing to be recharged. The newly developed battery pack could be directly lifted into the chassis and connected after delivery. The solution is powerful, reliable, and offers a significant reduction in ecological impact. Theo Mastenbroek emphasizes the increased efficiency and reliability of electric HPU’s: “Much less maintenance is required for electric HPU’s. In addition, they operate more quietly and without smelly exhaust gases!”
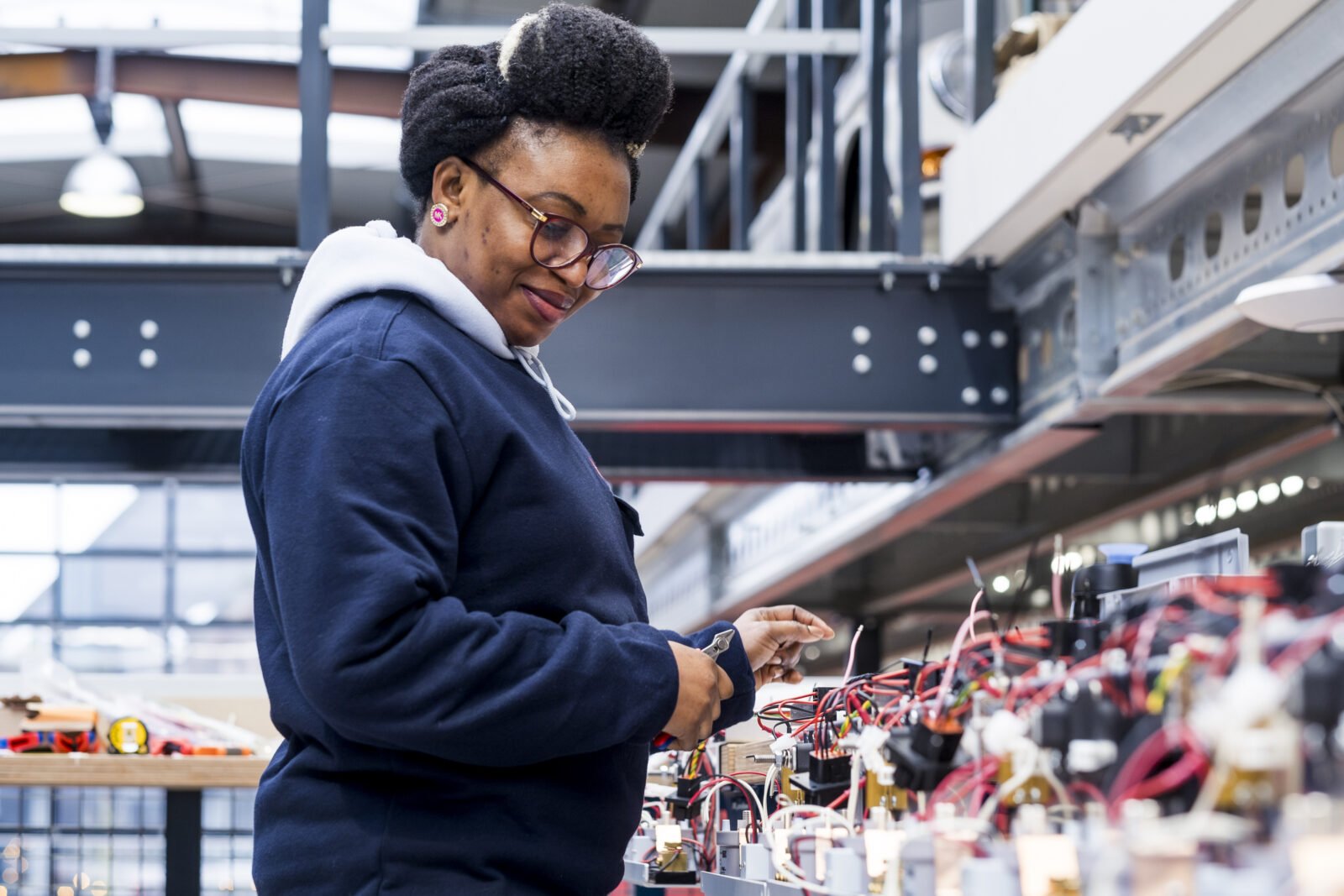
"*" indicates required fields